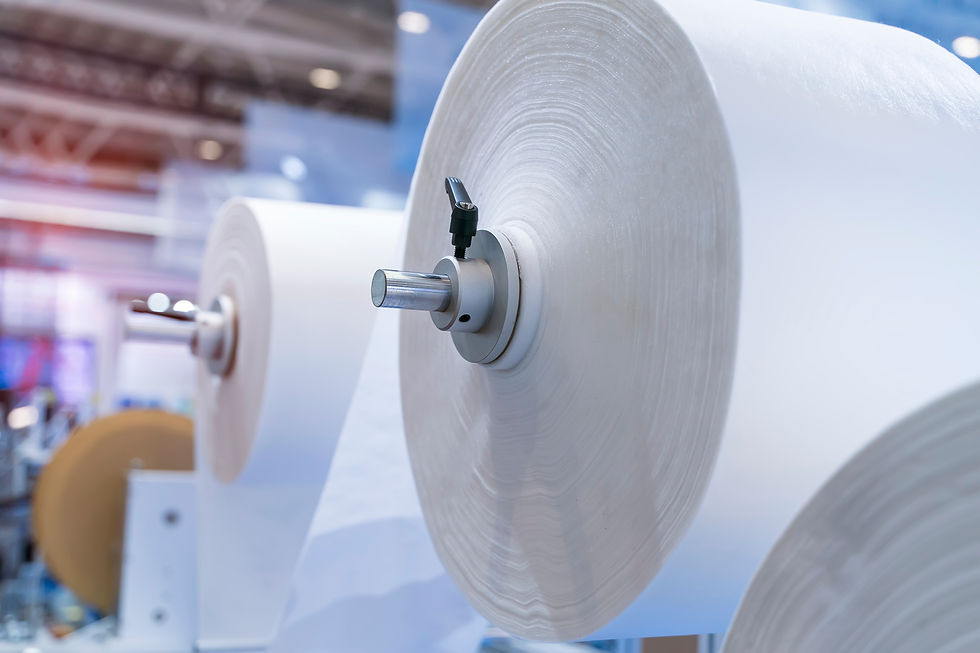
INDUSTRIAL FILTRATION
Filtration is the process of passing a fluid through a porous material, causing particles that contaminate the fluid to become trapped in the material. This results in a cleaner fluid. Industrial fluids are filtered to remove metallic particles created by the manufacturing process. Removing the particles will extend the useful life of the fluid, and reduce the cost of the manufacturing process.
-
Furniture
-
Geotextiles
-
Healthcare and Pharmaceutical
-
Hydrocarbon Processing
-
Steel and Metal Working
Industries We Serve:
-
Automotive
-
Agriculture and Landscaping
-
Air Filtration
-
Aluminum Canning
-
Aviation & Aerospace
-
Construction
-
Food/Industrial Frying

INDUSTRIAL FILTRATION
Filtration is the process of passing a fluid through a porous material, causing particles that contaminate the fluid to become trapped in the material. This results in a cleaner fluid. Industrial fluids are filtered to remove metallic particles created by the manufacturing process. Removing the particles will extend the useful life of the fluid, and reduce the cost of the manufacturing process.
There are four important characteristics of filter media: strength, pore size, capacity, and chemical compatibility.
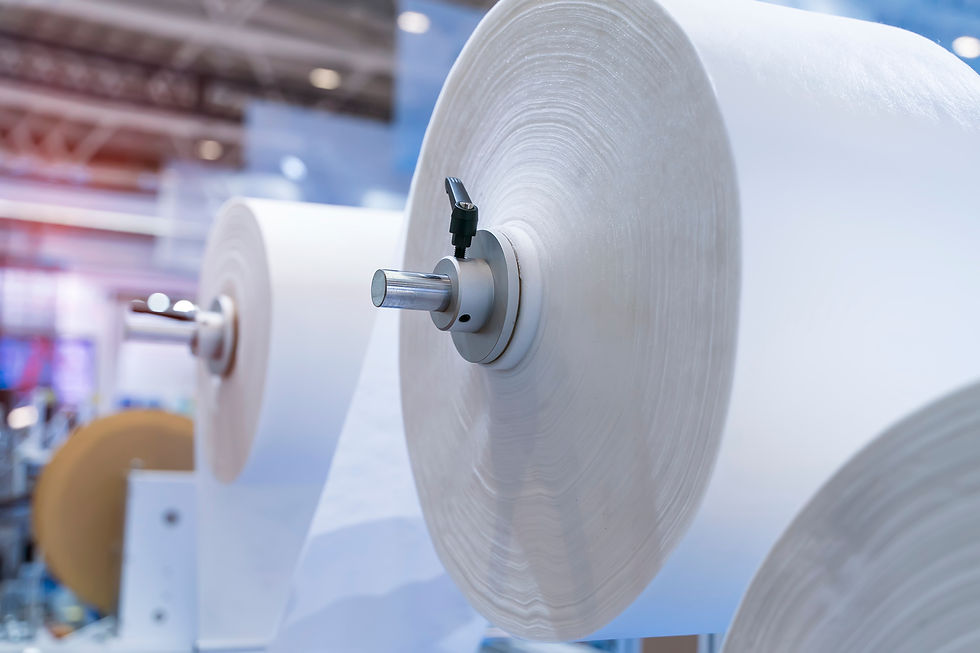

Other factors that affect the strength of the filter media's web:
-
Synthetic fibers are stronger than cellulose fibers.
-
A web with long fibers will be stronger than one with short fibers.
-
A heavier web, with greater mass, will be stronger than a lighter weight web.
-
Spunbound webs with thermally bonded fibers are stronger than wet laid or carded webs that have chemically bonded fibers.
The Mullen Test measures the force necessary for a blunt object to burst a sample of filter media. Expressed in pounds per square inch, the test may be run on either wet or dry samples. The greater the strength, the less likely the medium will burst while subjected to the stresses of the filtering process.
The Tensile Test measures the longitudinal strength of a sample of the filter media. Grab Tensile measures this strength when a sudden pulling force is exerted in the plane of the filter media. The results are expressed as the pounds of force needed to cause the sample's web to break.
The Mullen Test predicts the ability of the Web to refrain from bursting during the filtration process, while the Tensile Test predicts the ease with which the dirty filter paper will be extracted from the filter equipment.
STRENGTH
Any material used to filter metal working fluids must be strong enough for the process. The best filter membrane in the world is useless if it falls apart. Two tests of fabric strength are important measurements of its suitability for the application. They are the Mullen and Tensile strength tests.
Factors that effect pore size:
Fiber Size - the most efficient filter media are made with varying fiber diameter fibers.
Web Formation - webs with uniform fiber distribution will have smaller pores than webs with widely random distribution.
Mass - increasing the amount of fibers in a non-woven will reduce the average pore size and improve efficiency.
Density - increasing the density of a media's web tends to compress fibers and reduce the average pore size.
Fiber Chemistry - polypropylene fibers are highly attractive to oil. In dense webs this tends to cause the media to be rapidly coated with oil, preventing the passage of coolant and shortening filter life. But in more porous structures the fibers can be coated with oil without the media surface blinding. These oil coated fibers act like fly paper. The particulate then clings better to the fibers.
PORE SIZE
The pore size of a filter reflects the average pore through which the fluid must pass. The smaller the pore, the more efficient the filter media will be, enabling it to remove smaller particles. This is sometimes called the nominal micron rating.
The nominal micron rating is not a useful measurement of pore size. It is an arbitrary number listing the size particle, in microns, which a filter media is supposed to be efficient at removing from the fluid. The number has no basis in reality. But it is often accepted as gospel.
Only by testing a filter media, under specific conditions, can it be determined if it is the correct media for that application.
CAPACITY
The capacity of a filter medium reflects the amount of contaminant which the medium will capture within its pores before the flow is restricted sufficiently to cause the filter to index. One can determine the amount of dirt removed by a filter, by measuring capacity of a filter media, and knowing how many yards of media are used in a day.
Important factors when designing high capacity filter:
Caliper - the caliper or bulk of a filter web is measured in thousandths of an inch. A thicker membrane will have greater capacity than a thin filter medium. A thick web provides greater opportunity for vertical as well as horizontal flow through the filter allowing particulate to be captured without restricting fluid flow.
Fiber Size - smaller fibers will create more fiber layers and greater capacity for horizontal as well as vertical fluid flow.
The filter media with the greatest capacity will exhibit lower usage than a product of equivalent efficiency but lower capacity. With growing concerns regarding the disposal of spent filter media, increasing filter media capacity is critical.
It is important not to confuse filter capacity with filter life. A filter medium with high capacity will often exhibit longer filter cycles, but filter cycles alone are not a measure of capacity. The capacity of a filter measures the amount of containment retained by the media and is expressed in grams per area. Filter Life is only a measurement of the length of time between filter cycles.
CHEMICAL COMPATIBILITY
The capacity of a filter medium reflects the amount of contaminant which the medium will capture within its pores before the flow is restricted sufficiently to cause the filter to index. One can determine the amount of dirt removed by a filter, by measuring capacity of a filter media, and knowing how many yards of media are used in a day.
Important Considerations for the Media Designer Include:
Binders - most webs with short staple fibers require chemical binders to bond the fibers together. The wrong binder can be dissolved by the coolant, leaving a slurry of fibers floating in coolant.
Fiber Selection - the most commonly used filter media fibers are polyester, cellulose and polyolefins (including polyproplylene and polyethylene).
Polyester has the broadest application. It is available for all manufacturing processes, has good strength characteristics and is suitable for a wide range of chemicals.
Cellulose fibers are short, require chemical binders and are not suitable when very high strength is required.
Polyolefin fibers are used in all but the wet laid (paper) forming process. The fiber can be extruded to very fine diameters, has excellent chemical resistance to wide range of acidic and caustic fluids, and has very good strength characteristics.
High strength and chemical resistance have been easily attainable for a long time but the combination of both high filter efficiency and high dirt holding capacity has eluded filter media designers for years. Most webs were either efficient at removing smaller particles or had very long filter cycles while removing only the larger contaminant. The best of both worlds consists of laminating a highly efficient filter paper to a paper with high capacity

2146 Avon Industrial Dr.
Rochester Hills, MI 48309
248.844.1239