CRYSTAL FILTRATION IMPROVES HONING FILTRATION FOR AN AUTOMOTIVE MANUFACTURER
- Crystal Filtration
- Jan 4, 2024
- 3 min read
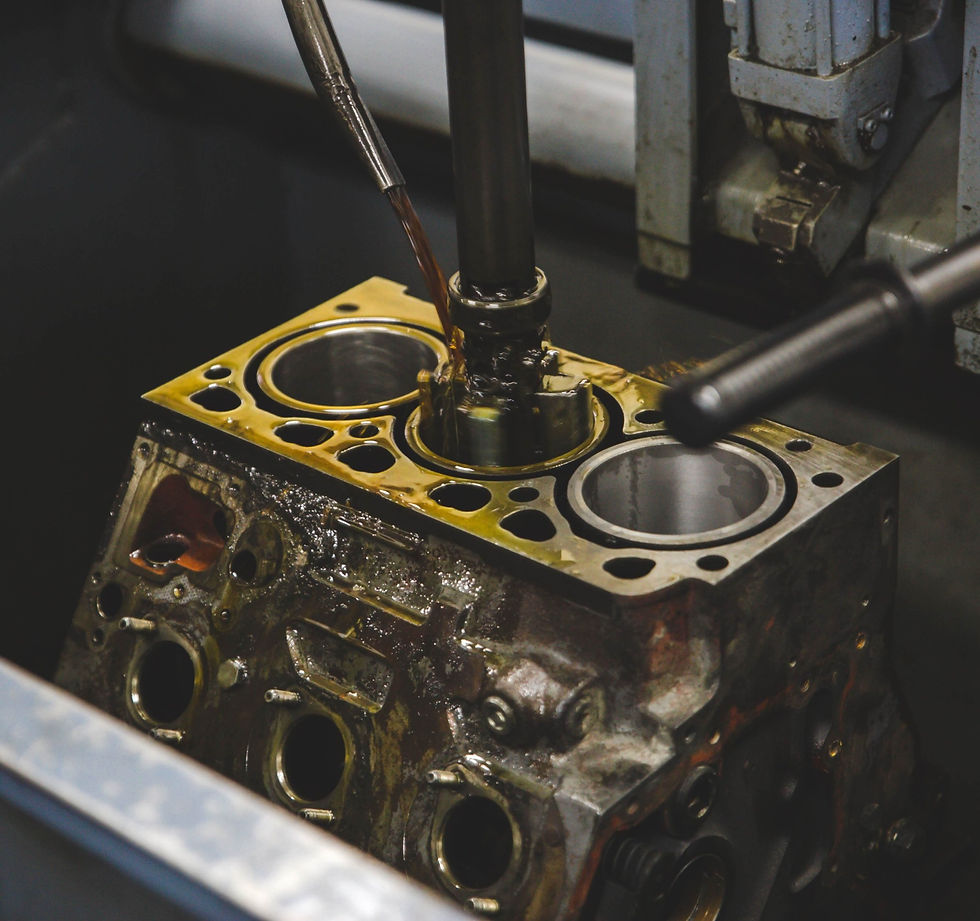
The honing application proves to be the most critical in the manufacturing process with common uses including the finishing of blocks, cylinders, liners, and gears. A very fine particulate is generated, requiring effective filtration. Crystal Filtration's engineers were able to improve coolant clarity, provide longer media life resulting in lower monthly media costs, and an improved process.
The Challenge
An automotive plant, operating at only half its daily production target, was on the path to encountering a bottleneck on the filter in line with a honing system.
Using a competitor's filter media, filter indexing occurred every 12 minutes and the succeeding clean tank took 7 minutes to fill. The gap between index and fill times being so close poses a serious problem. With an increase in production, more dirt would be introduced into the coolant causing the filter to reach capacity sooner, decreasing index times. Indexing times closing in on the time it takes to fill the clean tank threatens shutting down the line by starving the clean tank of coolant and preventing honing machines from running.
Crystal Filtration’s Strategic Approach
Understanding the constraints of not being able to change the flow rate or filter area, Crystal Filtration’s technical sales engineers collaborated with the honing engineering team. The key to resolving the issue rests in identifying the correct filter media that could address the impending challenges as production scaled up.
Path to the solution:
1. Benchmarking
The first step involved collecting coolant samples to establish a benchmark for the dirt count in the clean coolant going back to the machines based on existing filter media.
Simultaneously the team tracked the frequency and volume of media indexing, laying the groundwork for a comprehensive solution.
2. Laboratory Testing
With coolant samples at Crystal Filtration's lab, several engineered filter medias were tested by a ppm report, multi pass, and life/efficiency to determine Crystal Loft 50 had the best potential to improve clarity and increase capacity.
3. Field Trials
With Crystal Filtration's technical sales engineers on-site, Crystal Loft 50 was trialed in comparison to the automotive plant's standard media.
The team recorded index times, length of media per index, and collected coolant samples over several days to evaluate the effectiveness of Crystal Filtration's Crystal Loft 50 media.
The Results
Crystal Filtration's solution yielded optimal results including increased filter index times, enhanced clarity, and cost savings.
Increased Filter Index Times
The new filter media improved cycle times by 30-40%, ensuring a more streamlined production process.

Enhanced Clarity
The coolant clarity had a 5% improvement with Crystal Loft 50 vs. the competitor's filter media, indicating a more efficient removal of contaminants.
Cost Savings
Crystal Filtration not only provided superior filter media but did so at a price 35% less than the competitor’s media being used. This significant cost saving underscored the financial benefits of the implemented solution.
Conclusion
Crystal Filtration's success story in process improvement and cost savings for the automotive manufacturer showcases the power of strategic filtration solutions. By identifying the correct filter media and conducting meticulous trials, the team not only resolved the present and impending challenges but also delivered lasting efficiency gains at a reduced cost. This case study exemplifies the importance of customized solutions in optimizing manufacturing processes for long-term success.
If you are interested in partnering with a filter media supplier who has a proven track record of delivering solutions that result in cost savings and process improvements, contact us at www.crystal-filtration.com or sales@crystal-filtration.com to connect with one of our technical sales engineers.
Comments